Products and Services
We offer a wide range of Architectural Precast Concrete products and services. Whether you’re looking for feasibility advice and cost planning, information about concrete colours and finishes or a detailed design service for your project we can help.

Preconstruction Advice / Feasibility
We can help you transform your ideas into reality. We provide feasibility and pre construction advice on a wide range of subjects to ensure that your vision is achievable, cost effective and sustainable.
Early engagement will allow us to advise you on:
- Concrete colour and surface finish possibilities.
- Cost advice
- Lead in and on site programme durations
- Access methodology and logistical requirements
- Panel sizes and anticipated joint locations
- Panel weight and loadings
- Typical fixing details showing how PCC elements can be fixed to primary structure.
- Thermal Performance
- Embodied Carbon
Wondering how our expertise in precast architectural concrete fits into your plans? Contact us for an appointment without any obligation.
Design & Technical
Our Engineers will give cognisance to the structural requirements for every element we produce, at each stage of its life, from initial demoulding and handling stresses, through transportation and installation considerations and, finally, relative to its performance in use.
Below are just some of the issues which have to be addressed and/or considered within the development of the detailed design:
- Reinforcement – Design and Configurations fully supported by structural calculations.
- Load Bearing or Non-Load Bearing
- Structural or Non-Structural
- Stacked or Individually Supported
- Live Loads and Dead Loads
- Wind Loads and Snow Loads
- Exposure Conditions (Location)
- Design and Service Life Requirements
- Building Movements (Thermal, Deflections, Etc.)
- Building Tolerances
- Thermal Performance and Condensation Risk Analysis
- Joint Design and Movement Accommodation Factors (MAF)
Manufacturing
Architectural concrete is an exciting material that combines functionality with visual impact. Its aesthetic and architectural uniqueness, combined with its structural capabilities, endears it to both architect and builder, alike, and offers almost endless potential uses as a modern method of construction.
Some of the additional services that we provided :
Ancillary Services – Insulation / Firestop / Joint - Surface Treatments / Windows, balconies, balustrades

Products & Properties
So what are the distinct and notable benefits of using Architectural Precast Concrete….
- Almost anything is possible: The flexibility afforded by concrete in its fluid state combined with advanced formwork techniques means that it can be shaped to realise even the most intricate of architectural visions.
- Time and Cost Savings: through factory controlled off-site manufacture of prefabricated elements by coordinating just-in-time deliveries to suit the client's logistical and programme requirements on-site. It is also possible in conjunction with other specialist trade contractors to pre install at our factory windows, Juliet balconies, balustrades and the like into our elements. Additionally, production as well as these ancillary off-site activities are much less likely to be hampered by adverse weather conditions.
- Inherent Characteristics: Durable, impact resistant, non-combustible, high thermal capacity, excellent acoustic properties, colour consistent due to the primary use of naturally occurring sands and aggregates, easy to care for and sustainable.
Colours
Architectural concrete is available in a wide range of colours. Your creativity is given carte blanche.
Surface Finishes
Architectural Precast Concrete elements, from Decomo, can be produced in a number of different surface finishes and textures.
Together with the almost unlimited choice and aggregates and/or pigments the aesthetic versatility and durability of our products is ensured. Additionally, the incorporation of facing materials such as bricks, natural stone, terracotta or tiles/ceramics can provide an alternative dimension and range of options.
Acid Etched
This finish is produced by applying (usually by brush) a diluted solution of hydrochloric acid to the required surfaces. In some instances, it may be appropriate to apply the solution in a gel form or to even ‘dip’ the element into an ‘acid bath’. In all cases, the surfaces are thoroughly rinsed with clean water to further dilute the ‘run-off’ and to ensure no acidic residue is left.
Acid etching removes the surface laitance of the concrete and leaves a fine granular texture. The degree of texture can be varied by the length of time the solution is left before rinsing off, the strength of the solution or the number of applications.

Faced
Decomo can produce elements faced with inlays of bricks, natural stone, terracotta or tiles/ceramics.
The inlays are placed ‘face outwards’ against the requisite mould surfaces and when positioned in a vertical plane will be secured through the formwork to ensure there is no movement or displacement when pouring the backing concrete. Where appropriate, ‘keys’ will either be pre-formed or cut into the rear face of the inlays or stainless steel pins may also be used.
The joints between the various forms of inlay will, generally, be post pointed with selected mortars following demoulding and any other form of finishing required.

Gritblasting
Using a high-pressured air supply to blast the required surfaces with either sand or grit particles, the surface laitance of the concrete is removed to expose the fine and/or coarse aggregates depending upon the extent of blasting.
As this is an ‘abrasive’ finishing technique, even a light blasting will still provide a rougher texture of finish than acid etching.

Polished/Honed
Polishing (or honing) is carried out using our ‘state of the art’ polishing machines, Whether flat panels, circular columns or, simply, irregular or intricate shapes and configurations, Decomo has the right equipment for any application.
The polishing is carried out in stages with the first ‘pass’ of the polishing head, with an ‘aggressive’ diamond tipped pad fitted, removing approximately 3mm from the surface and, essentially, cutting through the aggregates. An allowance for this ‘removal’ is made when dimensioning Production Drawings for the elements.
Subsequent ‘passes’ are made using ever finer polishing pads until the required level of sheen is achieved. A polish, similar to that used on marble, may also be applied.
For honed finishes, the number of passes are limited with the final finish remaining matt with some coarseness to the texture still being discernable.
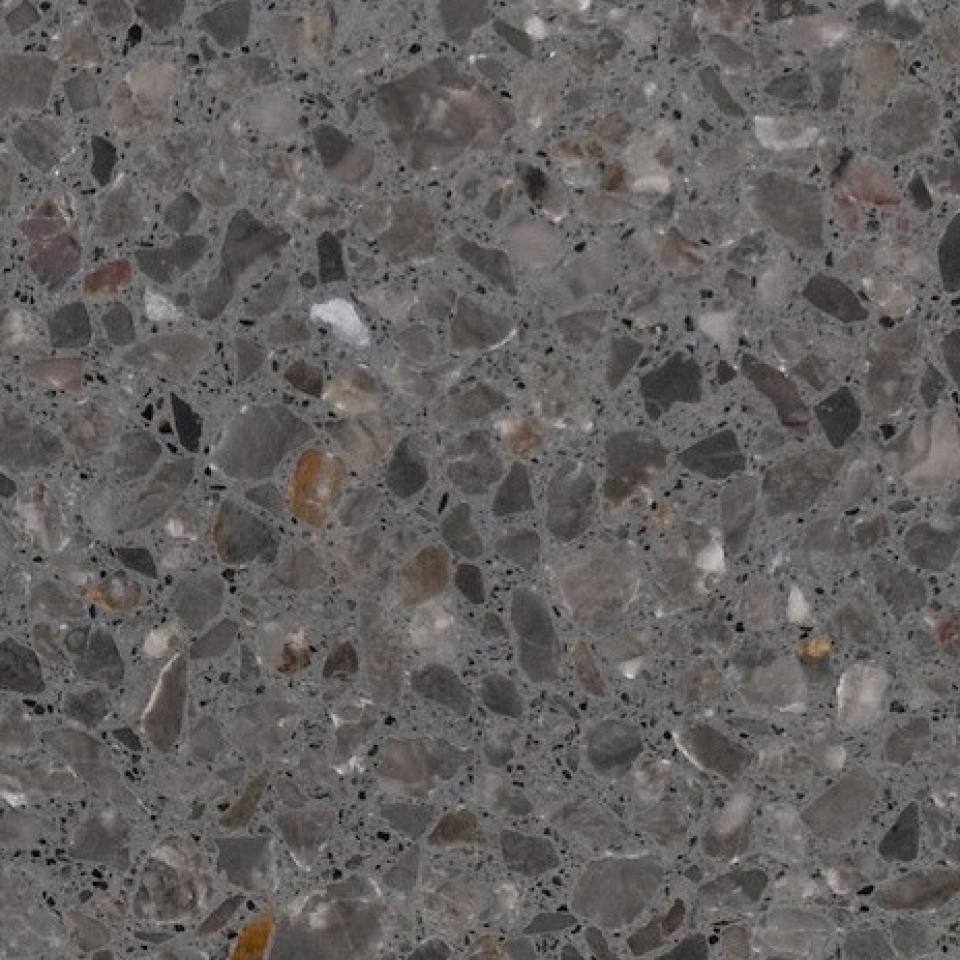
Structured
A structured appearance may be formed by creating a ‘negative relief’ pattern on the requisite surfaces of the mould or formwork or by utilising a patterned mould liner. These liners are, generally, in the form of rubber mats incorporating either ‘off the shelf’ or custom designs and will, usually, be procured from specialist suppliers of the likes of www.reckli.net.

Retarded
Retarders may be applied to the mould or formwork from which an element is to be cast or may, equally, be applied, directly, onto the required surfaces of the fresh concrete.
In both situations, these surface retarders, which are also often referred to as “deactivators”, chemically delay the set of the concrete, to a controlled depth, by slowing or stopping the hydration process. The remaining depth of concrete will cure and harden normally without affecting the setting time or strength gain.
The un-hardened cement/sand matrix is removed from the surfaces by washing away with pressured water, leaving the coarser aggregates exposed.
The depth of retardation and, hence, the degree of aggregate exposure is controlled by selecting the appropriate strength of retarder.

Installation
Decomo UK Ltd.’s directly employed Management Team, with offices in London but covering the whole of the UK, includes a number of specialist Site and Project/Construction Managers thus enabling the planned, safe and controlled execution of all on-site installation activities, any temporary works and all related administration.
Health & Safety
Throughout our organisation, great emphasis is placed upon Health and Safety. Our UK based Directors possess IOSH qualifications with our Site and Project/Construction Managers, variably, holding SMSTS and NEBOSH qualifications as well as being appointed Persons or Crane and Lifting Operation Supervisors.
All works will be subjected to detailed and careful planning, with cognisance to CDM considerations, and will be covered by comprehensive Risk Assessments, Method Statements and/or Task Plans.
Furthermore, we fully support the principles set out within the ‘Code of Practice for The Safe Installation of Architectural and Structural Precast Concrete’ which Decomo UK Ltd was heavily involved in the drafting of.
Ancillary Services
In addition to the supply and installation of our products we can also provide complimentary ancillary products and services.
Read on for further advice ...
Thermal Performance and Insulation
Due to its inherent high Thermal Mass, concrete will naturally limit heat loss from a building during cooler periods such as winter and at night whilst it can retain a pleasant and cool indoor climate in the summer months.
Further insulation and a vapour control layer is typically, however, incorporated into the fabric of most external wall constructions and Decomo are able, where required, to pre-install this to cladding elements and the like in our factory prior to delivery; thus reducing, further, the programme allowances needed for carrying out such works on site. All insulation will be non-combustible.
Alternatively, insulation can, actually, be incorporated within the cladding elements in the form of ‘sandwich’ or ‘double skin’ panels where the insulation is located between an external aesthetic outer ‘leaf’ of concrete and a thicker structural inner ‘leaf’ which typically will act as a load-bearing or ‘stacked’ form of construction.

Acoustic Performance
Acoustic insulation in a building is of fundamental significance to the health and well-being of its occupants.
Specific requirements apply to different types of building and these are covered by various standards and regulations.
Typically, Decomo will contribute to the acoustic performance of a building by ensuring that any Firestop or Cavity Barriers incorporated within its Works are, in addition to their primary function, also tested for their sound insulation properties.
Water and Air tightness
The importance of correctly designing and selecting the right product for the joints between precast elements should not be under-stated or overlooked. Decomo will ensure the best solution, balancing aesthetic considerations with performance requirements, is always found.
Often the architectural desire will be to have, particularly, narrow joints but this must be tempered with the need for construction tolerances to be accounted for along with the movements that will occur within the building both during use and over time. Such considerations are addressed within the joint design as the Movement Accommodation Factor or MAF.
Equally, cognisance to the application methodology and any restrictions to same must be factored into any joint detail. Excessively recessed joints can present problems with application and the resulting performance of the joint.
Compatibility of the jointing product which, commonly, will be a silicone sealant, with the composition and finish of the substrate is, equally, of vital importance. Decomo will carry out extensive testing prior to selecting any particular product. Such tests will determine the adhesive, cohesive properties of the product together with identifying and potential migratory staining issues.
Joints will usually comprise either a single or double seal in accordance with the recommendations of BS 8297:2017. On occasions a third seal may be introduced in particular circumstances. Weep holes may also be required by the design.
Vapour Control Layers or VCL’s can also be incorporated into Decomo’s Design and Scope of Works. These may be in the form of a foil backing to any insulation provided with all joints being taped or by an independent membrane.

Non-Combustibility and Fire stopping
Architectural Precast Concrete is non-combustible and all elements manufactured by Decomo meet the requirements for a Euro Class A1 Rating without the need for testing as defined by BS EN 13501-1:2018.
Concrete does not contribute to fire by acting as a fuel nor does it give off toxic fumes or smoke. Compared with many other forms of construction, it represents the ‘safe choice’ when considering the risk of fire and the consequences of this to human life.
Decomo will not incorporate any combustible products within its design and, where required as part of its scope of works, provide Firestops or Cavity Barriers as passive means of fire protection to limit the spread of flames and smoke from any other potential fire source.
Window, Balconies, Balustrades
Decomo is accustomed to working closely and collaboratively with other specialist subcontractors to facilitate the off-site installation, at our production facility in Belgium, of the Window, Balconies, Balustrades and the like prior to dispatch of the completed composite elements to site.
Alternatively, we can coordinate designs with such other specialists to allow for cast in fixings to be introduced into our elements to suit post fixing of these components on site.
Maintenance
Any construction material can be susceptible to the effects of environmental contamination and graffiti.
Decomo advise Clients to consider the application of protective treatments to exposed surfaces, generally, in the form of anti-graffiti coatings, which can be permanent or sacrificial, at ground level and/or other accessible areas and weathering coatings at upper levels.
We can assist in the selection of appropriate products. With particular regard to Anti-Graffiti treatment, we believe this to be best carried out as an on-site application, by a specialist contractor offering full on-going support and maintenance services. Furthermore, this is likely to be required to the building, as a whole, and not only the Architectural Precast Concrete elements.
Notwithstanding the above, in certain circumstances, it may be appropriate and/or required by the Client for Decomo to undertake these works, ourselves and, in such instances, consideration will be given, not only to product selection, but, importantly, the timing and manor in which the coatings are to be applied; namely, in our factory prior to delivery of individual elements or on site, as a whole, once all components have been installed.